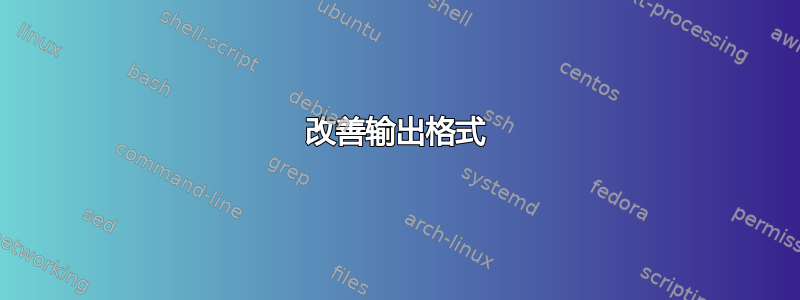
有人能看一下 pdf 格式的输出,并告诉我有什么方法可以避免第 1 页和第 3 页末尾出现这么多空白吗?抱歉发送了所有代码,但查看最终输出是必要的。
\documentclass[12pt]{article}
\usepackage[top = 1in, bottom = 1in, right = 1in, left = 1in]{geometry}
\usepackage{amsmath}
\usepackage{siunitx}
\usepackage{booktabs}
\usepackage{graphicx}
\usepackage{float}
\begin{document}
\begin{titlepage}
\newcommand{\HRule}{\rule{\linewidth}{0.5mm}}
\centering
{\scshape\LARGE University College Cork\par}
\vspace{1cm}
{\scshape\Large CE 2001: Lab Reports\par}
{\scshape\large Dr. Virkam Pakrashi\par}
\HRule
\vspace{0.4cm}
{\huge \bfseries \#1: Simply Supported Beam\par}
\vspace{0.4cm}
\HRule
\vspace{1.5cm}
{\large
\begin{tabular}{@{}l@{}}
\Large\textbf{Authors:}\\
David \textsc{O'Sullivan}\\
Yuriy \textsc{Lishchynskyy}\\
John \textsc{Kearney}\\
Billy \textsc{O'Connor}\\
Eoghan \textsc{Kelleher}
\end{tabular}
\par}
\vspace{4cm}
{\large \today\par}
\vfill
\end{titlepage}
\tableofcontents
\section{Objectives}
\begin{itemize}
\item To calculate the stiffness parameter of a beam via the load-displacement graph and subsequently calculate the Young's Modules of the beam.
\item To calculate the displacement of the beam at it's midpoint under various quarter-span loading conditions.
\item To calculate and compare the theoretical and experimental displacement along the beam under one (1 kg) quarter-span loading condition.
\end{itemize}
\section{Equipment}
A cantilever beam is placed horizontally on two supports, one fixed and the other a roller allowing the user to adjust the beam length.
A dial gauge is used to measure the displacement along the length of the beam under various conditions of quarter-span loading.
The equipment setup is described perfectly by the following image.
\begin{figure}[H]
\centering
\caption{Setup}\label{tab:set}
\includegraphics[scale=0.1]{Pic1}
\end{figure}
\section{Procedure}
\begin{itemize}
\item Take dimensions of the beam ($B$, $D$, $L$), - rectangular cross section.
\item Read initial displacement values, $w_0$, at locations $x$.
\item Apply successive and equal load masses at both quarter spans.
\item For each mass loading: \begin{itemize}
\item Measure the vertical displacement at mid-span.
\item Plot a point on the load-displacement graph (Load = $m \times g$).\end{itemize}
\item Determine the stiffness parameter, k (slope of the load-displacement graph).
\item Theoretical stiffness value; rearrange to get E. (See equation (1) below)
\item Place a unit mass, $m$, (1 kg) at each quarter span.
\item Read the values of displacement, $w_1$, at the locations, $x$ (different locations along length).
\item Calculate theoretical values of displacement, use symmetry. (See equation (2) below)
\item Plot the values of the displacement over the length of the beam for both experimental and theoretical data.
\end{itemize}
\section{Results}
\subsection{Calculating Young's Modulus}
The following is a table of quarter-span masses applied to the beam, the total mass applied and the displacement observed at the centre point of the beam (i.e. 500 mm).
\begin{table}[H]
\centering
\caption{Displacement-Load table}\label{tab:t1}
\medskip
\begin{tabular}{ccc}
\toprule
Quarter-Span m (kg)& Total m (kg) & Displacement (mm) \\ \toprule
0.0 & 0.0 & 15.22 \\
0.1 & 0.2 & 14.9 \\
0.2 & 0.4 & 14.58 \\
0.3 & 0.6 & 14.23 \\
0.4 & 0.8 & 13.9 \\
0.5 & 1.0 & ? \\
0.6 & 1.2 & 13.25 \\
0.7 & 1.4 & 12.91 \\
0.8 & 1.6 & 12.58 \\
0.9 & 1.8 & 12.23 \\ \toprule
\end{tabular}
\end{table}
The values of mass in both the first and second column will be multiplied by the acceleration due to gravity ($g$) in order to convert them to the \textit{Weight} applied to the beam. The values for displacement in the third column are uncalibrated and therefore must be calibrated in order to plot the total load vs. displacement graph. These values must be calibrated against the value of displacement for zero loading conditions (row 1, column 3 in table above). Thus all subsequent values of displacement, for the various loads, will be calibrated against (i.e. subtracted from) 15.22 mm. \textbf{Note: The displacement for the quarter-span mass of 0.5 kg is not shown and will be addressed in the Discussion section}. The following graph of total load (column two times $g$) vs. displacement is then obtained.\vspace{-10pt}
\begin{figure}[H]
\centering
\caption{Load vs. Displacement}\label{tab:g1}
\vspace{-15pt}
\includegraphics[scale=0.6]{Graph1}
\end{figure}
The slope of the trendline obtained from the above graph is 5.91 \si{N.mm^{-1}}. This value refers to the stiffness paramter, $k$, in the equation:\\ \begin{equation}
\boxed{k \approx \frac{384EI}{11L^3}}
\end{equation}\\
Where $E$ is the Young's Modulus of the beam material, $I$ is the second moment of area of the beam and $L$ is the length of the beam. Now knowing $k$, the above equation can be rearranged and $E$ can be calculated. The beam parameters are as follows:
\begin{itemize}
\item Length (mm) = 1000
\item Width (mm) = 24
\item Height (mm) = 6
\item I (\si{mm^4}) = $432$
\end{itemize}
Rearranging equation (1) to find $E$ and subbing in for the above values and $k$ gives rise to:$$E = \frac{(11)(1000^3)(5.91)}{(384)(432} = 391 \si{GPa}$$
\subsection{Four Point Bending:}
The next section of the experiment involved applying 1 kg masses to each quarter span of the beam and then measuring the values of displacement at each position across the beam's length.
\begin{table}[H]
\centering
\caption{Displacements}\label{tab:t2}
\begin{tabular}{cccccc}\bottomrule
Station & $w_0$ (mm) & $w_1$ (mm) & Calibrated $w_0$ & Calibrated $w_1$ & $w_1 - w_0$ \\ \toprule
0 & 16.86 & 16.86 & 0.04 & 0.04 & 0.00 \\
1 & 16.71 & 15.76 & 0.19 & 1.14 & 0.95 \\
2 & 16.38 & 14.35 & 0.52 & 2.55 & 2.03 \\
3 & 15.98 & 13.50 & 0.92 & 3.4 & 2.48 \\
4 & 15.42 & 12.61 & 1.48 & 4.29 & 2.81 \\
5 & 15.22 & 12.27 & 1.68 & 4.63 & 2.95 \\
6 & 15.62 & 12.74 & 1.28 & 4.16 & 2.88 \\
7 & 16.37 & 13.89 & 0.53 & 3.01 & 2.48 \\
8 & 16.83 & 14.99 & 0.07 & 1.91 & 1.84 \\
9 & 16.93 & 15.96 & -0.03 & 0.94 & 0.97 \\
10 & 16.94 & 16.94 & -0.04 & -0.04 & 0.00 \\ \toprule
\end{tabular}
\end{table}
The values of $w_0$ and $w_1$ are calibrated against the average initial displacement at the supports (where no deformation occurs). This is calculated to be 16.90 mm. The theoretical displacement is defined by the following piecewise function:
\begin{equation}
\boxed{w_{Theory} =
\begin{cases}
\frac{Px}{6EI}(3aL - 3a^2 - x^2), &0\leq x\leq a \\
\frac{Pa}{6EI}(3Lx - 3x^2 - a^2), & a\leq x\leq L - a
\end{cases}}
\end{equation}
Using equations (2) one can find all the displacements along the length of the beam. For the beam used in the experiment, $a = \frac{1}{4}L = 250$ mm. $P$ is the load applied at both quarter-spans and in this case it was a constant 1 kg mass, i.e. a 9.8 N downward weight.
The following table may then be constructed. \textbf{Note:The values of $w_T$ are implicitly calibrated.}
\begin{table}[H]
\centering
\caption{Theoretical Displacement}\label{tab:t3}
\begin{tabular}{ccc}
\hline
Range & Location (mm) & $w_T$ (mm) \\ \hline
& 0 & 0.00 \\
$0\leq x\leq a$ &100 & 0.53 \\
&200 & 1.00 \\ \hline
& 300 & 1.37 \\
&400 & 1.58 \\
$a\leq x\leq L-a$&500 & 1.66 \\
&600 & 1.58 \\
&700 & 1.37 \\ \hline
& 800 & 1.00 \\
$L-A\leq x\leq L$&900 & 0.53 \\
&1000 & 0.00 \\ \toprule
\end{tabular}
\end{table}
The following graph plots the $w_T$ and $w_E$ ($w_1 - w_0$) against the various beam positions.\begin{figure}[H]
\centering
\caption{Graph of $w_T$ and $w_E$.}\label{tab:g2}\vspace{-20pt}
\includegraphics[scale=0.6]{G4}
\end{figure}\vspace{-20pt}
The various graphs and trends will be discussed in the Discussion section of this report.
\section{Discussion}
Relevant measurements were kept in mm as this was the standard unit on the dial gauge that monitored deflection. This sustained a uniformity across the experiment and report.
\subsection{Young's Modulus}
The ends of the beams had a displacement of 16.86 mm and 16.94 mm respectively. This is a difference of 0.08 mm. This was not expected seeing as the deflection at both endpoints should have been 0 mm. This discrepancy is most likely due to residual stresses left in the beam after repeated loading. This was easily dealt with in the calculations by averaging the two values to give a value against which the other readings could be calibrated.
There were no 0.5 kg masses available to use for this section of the experiment and thus there is a vacant data point in figure 2 above. The value of displacement for the 0.5 kg quarter-span loading condition (9.8 N total) can be simply read from the graph via extrapolation. This yields a value of approximately 1.65 mm. Or, alternatively the value of 9.81 N could've been subbed into the equation of the line for the Load-Displacement graph and thus $x$ could've been solved for.
\subsection{Four Point Bending}
Max displacement always occured at the midpoint of the beam, regardless of the fact that the point masses were placed at each quarter-span and not the midpoint, this can be proven by differentiating equation (2), on the latter interval, with respect to x and letting the derivative equal to 0. \begin{equation}
\boxed{\frac{dw_T}{dx} = \frac{Pa}{6EI}(3L - 6x)}
\end{equation}
Letting this equation equal to 0, it can be found that $x = \frac{L}{2}$ when $w_T$ is at a maximum.
It was first observed that the beam was not at a constant displacement across it's length, i.e. the calibrated values of $w_0$ increased as one moved from the beam support to it's midpoint. This initial displacement of the beam is due to it's self weight.
The difference in the values of $w_T$ and $w_E$ is due to the beams self weight and the fact that it is not factored into the calculation of $w_T$ whilst it is included in the $w_E$ term, thus there is a difference in the graphs of $w_E$ and $w_T$ figure 3. The difference in $w_E$ and $w_T$ will therefore be approximately equal to the deformation caused by the self weight of the beam.
A clear symmetry was noted in the displacement across the length of the beam for both self-weight and point-mass loaded conditions. This symmetry took the form of a linear change in deflection approaching the midpoint from the right and left hand side. This was as the loads were symmetrically placed about the midpoint.
\section{Conclusion}
\begin{itemize}
\item The value of $E$ was found to be 391 GPa, which is extremely large. From this value, one could conclude the beam to be made of Tungsten. This a wild guess though seeing as the value of $E$ would decrease greatly upon increasing the dimensions of the beam (see rearranged equation (1)). Thus, while it is possible that the beam material is Tungsten, it could really be a number of other materials.
\item There were very few errors/unexpected values found in the experiment as most values showed expected trends.
\item A linear relationship was found between the applied load and the induced displacement at the midpoint of the beam.
\item It was proven that the maximum displacement in a simply supported beam occurs at the midpoint.
\end{itemize}
\end{document}
答案1
由于无法访问您使用的图像文件,因此无法准确地重新创建您的文档,因此无法对您的问题给出明确的答案。
一些建议部分呼应了之前的评论中提出的建议:
不要使用
[H]
浮点位置说明符。相反,请尝试[htb!]
。检查一些图形的边缘是否包含大量空白。如果是,请弄清楚如何修剪不需要的空白。这应该会使外观更紧凑。
\raggedbottom
在序言中发布该指令。
一些进一步的评论主要涉及编程和编码效率以及您所使用的某些宏的最佳使用:
您似乎对许多对浮点数和方程式的交叉引用进行了硬编码,即使这些对象被赋予了
\label
s。您会发现,\ref
在交叉引用这些对象时使用该命令几乎从一开始就可以为您节省大量时间。同样,在提及数量及其单位时,不要写如下内容
5.91 \si{N.mm^{-1}}
相反,写
\SI{5.91}{\newton\per\milli\meter}
如果没有其他问题,使用
\SI
宏将避免在数量和单位之间遇到不必要的换行符。不要
$$
在 LaTeX 文档中使用。相反,使用\[
和\]
来分隔未编号的显示方程。请参阅帖子为什么 \[ … \] 比 $$ ... $$ 更可取?了解有关此主题的更多信息。
最后但同样重要的一点是,我建议不要在标题页上拼错老师的名字(“Virkam”?!)。