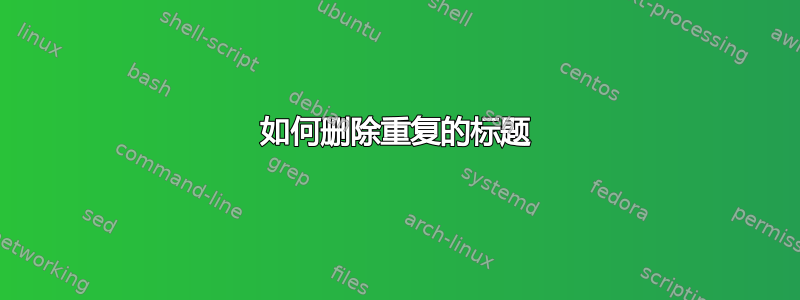
每两页出现一次“图表列表”。如何删除它?
%%%%%%%%%%%%%%%%%%%%%%%%%%%%%%%%%%%%%%%%%%%%%%%%%%
\documentclass[b5paper, 11pt, openany, titlepage]{book}
%%%%%%%%%%%%%%%%%%%%%%%%%%%%%%%%%%%%%%%%%%%%%%%%%%
\usepackage[pdftex]{graphicx,color}
\usepackage[cp1250]{inputenc}
\usepackage{indentfirst}
\usepackage[numbers,sort&compress]{natbib}
\usepackage{geometry}
\newgeometry{tmargin=3.6cm, bmargin=3.6cm, lmargin=3.2cm, rmargin=3.2cm}
\usepackage{multirow}
\usepackage{amsmath}
\usepackage{amssymb}
\usepackage{pdflscape}
\usepackage{float}
\usepackage{adjustbox}
\usepackage{etoolbox}
\usepackage[hidelinks]{hyperref}
\usepackage{chapterbib}
\usepackage{booktabs}
\usepackage{suffix}
\usepackage{textcomp}
\linespread{1.5}
\usepackage{xspace}
\usepackage{textcomp}
\newcommand\degrees[1]{\ensuremath{#1^\circ}}
\renewcommand{\figurename}{Fig.}
\renewcommand{\tablename}{Tab.}
%%%%%%%%%%%%%%%%%%%%%%%%%%%%%%%%%%%%%%%%%%%%%%%%%%
\begin{document}
%\pagestyle{plain}
\newpage
%%%%%%%%%%%%%%%%%%%%%%%%%%%%%%%%%%%%%%%%%%%%%%%%%%
\setcounter{chapter}{1}
\chapter[]{An dfluence ofyyyyd into ddve manufactureddddd structure}
\textbf{yyyyyyyyyyyyyyyyyyyyyyyyyyyyyyyyyyyyyyyyyyy}
\newpage
\tableofcontents
\listoffigures
\newpage
%%%%%%%%%%%%%%%%%%%%%%%%%%%%%%%%%%%%%%%%%%%%%%%%%%
\section{Introduction}
%%%%%%%%%%%%%%%%%%%%%%%%%%%%%%%%%%%%%%%%%%%%%%%%%%
Additizxczcturing (AM)sdgsdgsgsditsgsdg Owing to the recent improvement in technology and the current trend toward a susdgsgadvancement of technolosdsdf
Mechanical characterisation of CFRP and pure polymer samples has been studied during the FDM process and has not undergone the 3D printed components itself, in several literature. Also, a few investigations were carried out for the temperature elevation effect on the mechanical behaviour of composite structures specifically to the heat deflection temperature of PLA. In this section, CFRP specimens were additively manufactured through FDM process and tested on an environmental chamber to investigate the effect of the temperature elevation on the mechanical behaviour of those samples. The fabricated specimens were also modelled in the Finite Element Analysis software package, ABAQUS in order to simulate the thermo-mechanical behaviour of the manufactured specimens under thermal loading. The resulted simuladfgdfgdghdgfhfhjghjlymers are explained in this chapter. Thereafter, the results given by both numerical and experimental studies are provided. Finally, the results are discussed.
\section{Material and Methods}
t feeding system. When filament reaches printing head which is heated up to 200 $^{\circ}$C polymer liquefies. Impregnated carbon fibsdsdf
In the middle of each sampledhfdhdfreinforcement direction.
A comparison of FBG sensor resulted in reduction of the sensor reflectivity level.
\section{Results and Discussion}
where indexes
A comparison of total strain due to exposition of samples to elevated temperatures is presented in dfdffdf. For bodfdffdfto the relatively low heat distortion temperature of PLA matrix. The strain levels determined for M3~X are one order of magnitude higher than for CFRP. Additionally, both FBG sensors in polymer material show almost the same strain values. On contrary to this, strain values determined by sensors in CFRP material differ. The embedded sensor shows the mean strain value in CFRP material. In the case of the attached sensor, tdfdfd partially on a matrix and a carbon fibre. Due to this, attached FBG sensor do not have to determine the real strain values in the whole analysed element.
\newpage
A comparison of total strain due to exposition of samples to sub-zero temperatures is presented in rrrrrrrrrrrrrrrrrrrrrrrrrrrrr
The material behaviour corresponding to thsfggdhfhjf the temperature on the CFRP sample was modelled using the Finite Element Method (FEM). The numerical calculations were performed using Abaqusgjn thjghgjgve in the y-direction and another side restricted in the x-direction in order to let the saerwerwetwrtion (CTE) of matrix. Such parameter was determined experimentally.
A comparison of strain values deteeryeryerylts are presented for the embedded sensor as the mean mechanical strain values for sfgdfghfghjhfor one time slot.
The mechanical strain values were calculated from the relationship
where $\varepsilon_{f}$ is a strain ijdghjghjghjghjghjghjghjntal results. The averaged percentage difference between fgdfanges, respectively.
\section{Conclusions}
In this paper, a comparison of two Ahjkhkk
The analyses of the temperatures (elevated and sub-zero) were concerned on both the material behaviour and the sensohkhjktrix or partially on a carbon fibre and a matrix.
A comparison between experihjlhljl
%%%%%%%%%%%%%%%%%%%%%%%%%%%%%%%%%%%%%%%%%%%%%%%%%%
\end{document}
%%%%%%%%%%%%%%%%%%%%%%%%%%%%%%%%%%%%%%%%%%%%%%%%%%