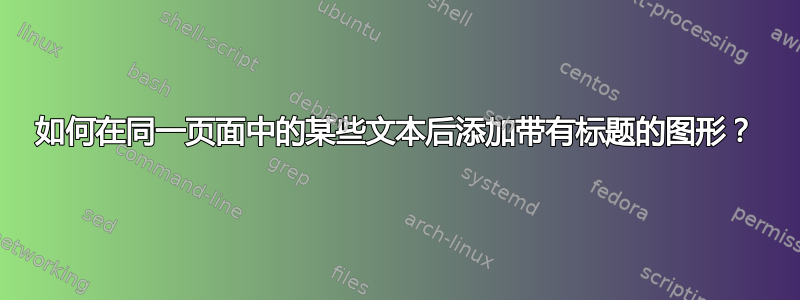
\documentclass[11pt]{article}
\usepackage[utf8]{inputenc}
\usepackage{listings}
\usepackage{amsmath}
\usepackage{amssymb}
\usepackage{graphicx}
\begin{document}
\section{Power Converter Topology and Electric Machine Selection}
\subsection{Power Circuit Topology}
The choice of power circuit topology in the design of an Integrated Starter Generator system is crucial. The associated power electronics technology used in power conversion within the ISG system has important considerations in its working capabilities in numerous applications.\\ \\
Here, either of the traditional Voltage Source Inverter or the Current Source Inverter can be used for the power conversion. A conventional VSI acts as a DC-AC buck inverter or an AC-DC boost rectifier which works with the constraint that the AC output voltage does not exceed the DC bus voltage while a conventional CSI acts as a DC-AC boost inverter or an AC-DC buck rectifier which works with the constraint that the AC output voltage is higher than the input DC voltage that is fed to the inductor. The diagrams for both the inverters are shown here [Figure 2.1 and 2.2]. Due to these constraints both topologies do not prove to be efficient method for optimal ISG design and functionality for the required situation.
\begin{figure}
\includegraphics[scale=0.75]{2-1.png}
\caption{Conventional VSI Topology}
\end{figure}
\\
The high-speed procedure of induction machines in expressed in [21] with the help of a dual voltage inverter control method. The primary motive of the control strategy discusses in to achieve a stable power region of 10:1 speed range under 42V and to alleviate the issue of low voltage limit. The control strategy works well in terms of allowing the system to perform over a very large speed range with induction machines of voltage less than 42V, however the extra inverter which is analogous to the main power inverter will raise system complexity, costs and system volume. A new power converter topology for series and parallel stator winding arrangements is expressed in [22] for large speed range for the ISG system. There are multiple disadvantages associated with the discussed configuration like transition from series to parallel, high rated converter power and significant realization efforts.
\end{document}
这会将我的图表移到新的页面上,而不是代码中我插入图表的位置。我该怎么做才能将图表保持在我想要的段落之间?
答案1
您可以通过在图形的位置声明后添加感叹号来强制浮动保持在原位。在这种情况下,您希望它位于文本中的确切位置,因此“此处”。因此您可以写 \begin{figure}[h!]。
您还应该删除 \\。
\documentclass[11pt]{article}
\usepackage[utf8]{inputenc}
\usepackage{listings}
\usepackage{amsmath}
\usepackage{amssymb}
\usepackage{graphicx}
\begin{document}
\section{Power Converter Topology and Electric Machine Selection}
\subsection{Power Circuit Topology}
Thee choice of power circuit topology in the design of an Integrated Starter Generator system is crucial. The associated power electronics technology used in power conversion within the ISG system has important considerations in its working capabilities in numerous applications.
Here, either of the traditional Voltage Source Inverter or the Current Source Inverter can be used for the power conversion. A conventional VSI acts as a DC-AC buck inverter or an AC-DC boost rectifier which works with the constraint that the AC output voltage does not exceed the DC bus voltage while a conventional CSI acts as a DC-AC boost inverter or an AC-DC buck rectifier which works with the constraint that the AC output voltage is higher than the input DC voltage that is fed to the inductor. The diagrams for both the inverters are shown here [Figure 2.1 and 2.2]. Due to these constraints both topologies do not prove to be efficient method for optimal ISG design and functionality for the required situation.
\begin{figure}[h!]
\includegraphics[scale=0.75]{2-1.png}
\caption{Conventional VSI Topology}
\end{figure}
The high-speed procedure of induction machines in expressed in [21] with the help of a dual voltage inverter control method.
\end{document}